I did some measurements to determine the accracy of the A4988.
There was a bit of a surprise that I found a large difference at intervals of 16 steps ( 16 microsteps mode). I repeated the test with on other pololu which showed the same effect. Is this normal? I’m missing something.
I measure with a 1.8 degr stepper and a 14 bit angle detector.
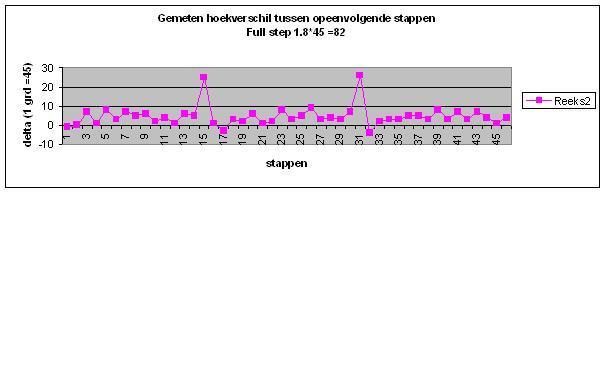
Hello.
It is unclear from the graph what you are measuring or what problem you are experiencing. What is the vertical axis of your graph? Could you describe the behavior you are seeing with your stepper motor when you are 1/16 microstepping? Could you tell also us more about the angle detector you are using?
- Jeremy
Microstepping is not intended to provide accurate steps, and does not do so. The torque is not constant either, so the motor can skip microsteps if too heavily loaded. Instead, microstepping is intended for smooth operation and avoidance of resonance effects. You can read more about microstepping accuracy here: micromo.com/microstepping-my … -realities
If you need more accurate positioning, use a toothed belt (preferred) or a geared drive.
Hello Jeremy, Jim,
The vertical axis:
This graph shows the difference between the calculated versus the angle measured with the help of a 14 bit position sensor.
The scale of the position sensor is from 0…16384 (14bit). So with a 1.8 degr stepper in 16 microstep mode this comes down to 5.12 per microstep on the scale of 0…16384.
Ideally I would expect a straight line and this is almost true except for a nice spike every 16 steps.
It was not the intention to measure the accuracy of the Pololu. I wanted to measure the accuracy and especially the linearity of the AMS AS5048 position sensor. I used a stepper as a tool to make a nice predictable rotation. There is no load at all; the magnet for the position encoder is glued at the motor axis. With a set of AS5048 position sensors we want to measure the actual dynamic behaviour at the robot tip.
As we use steppers in our 3D printers I wanted to have a look at the accuracy of microstepping. In the two samples I measured, there is a noticeable effect; when you know about it you can even hear the spike when the motor is turning at low speed.
I will have a look at the link to the realities link. Thanks a lot.
http://ams.com/eng/Products/Position-Sensors/Magnetic-Rotary-Position-Sensors/AS5048A
[quote]I used a stepper as a tool to make a nice predictable rotation.[/quote]As you can see, it does not. Notice in your plot that the peaks and valleys are matched, if you shift by 16. The encoder is much more accurate than the stepper.